Turbine Fan & Cooling Fan

Product Material
-
Metallic Material :Silicon Steel 35W300 (GB) / M300-35A (EN)
-
Insulating Material :PEEK, LCP, PBT,UL94-V0 (flame retardant)
The Strength of Ming-Li Company
With more than 3 decades’ experience in mold design and manufacture, stamping, injection molding, semi-assembly and assembly, our products are exported to Europe, the United State and all over the world!
The key elements for plastic injection Turbine Fan & Cooling Fan parts
When it comes to manufacturing plastic injection-molded turbine fan and cooling fan parts, several key elements need careful consideration to ensure optimal performance, efficiency, and durability. Here are the essential aspects to focus on:
-
Material Selection:
- Choose a plastic material suitable for fan applications, considering factors such as heat resistance, mechanical strength, chemical resistance, and dimensional stability.
- Common materials include engineering-grade plastics such as ABS, polycarbonate (PC), polypropylene (PP), and thermally conductive plastics for heat dissipation.
-
Design for Airflow Efficiency:
- Optimize the fan blade design and geometry to maximize airflow and pressure while minimizing noise and vibration.
- Consider factors such as blade profile, angle of attack, chord length, and blade pitch to achieve the desired airflow characteristics.
-
Mechanical Strength and Durability:
- Design fan parts with sufficient mechanical strength and rigidity to withstand dynamic loads, vibrations, and thermal cycling.
- Reinforce critical areas such as blade roots, hub connections, and mounting points to prevent premature failure or fatigue.
-
Heat Dissipation and Thermal Management:
- Incorporate features such as heat sinks, fins, or thermal conduction pathways to enhance heat dissipation and thermal management capabilities.
- Select materials with good thermal conductivity or add thermally conductive fillers to improve heat transfer efficiency.
-
Mold Design and Tooling:
- Design molds with precision to replicate intricate fan blade profiles and details accurately.
- Optimize mold cooling channels, gating systems, and ejection mechanisms to minimize cycle times and ensure consistent part quality.
-
Injection Molding Process Parameters:
- Fine-tune injection molding parameters such as melt temperature, injection speed, packing pressure, and cooling time to achieve complete filling of the mold cavity and minimize defects.
- Optimize process parameters to prevent issues such as flow marks, sink marks, warpage, or weld lines that could affect fan performance.
-
Surface Finish and Balance:
- Control surface finish to reduce air resistance and improve fan efficiency.
- Ensure that fan blades are balanced to minimize vibration, noise, and wear during operation.
-
Assembly Compatibility:
- Design fan parts with features that facilitate assembly, mounting, and integration into cooling systems or electronic devices.
- Ensure proper alignment, fit, and compatibility with mating components and mounting hardware.
-
Quality Control and Testing:
- Implement rigorous quality control measures throughout the manufacturing process, including inspection of raw materials, in-process checks, and post-molding inspections.
- Conduct functional testing and performance validation to verify airflow, pressure, noise levels, and efficiency of the fan parts.
-
Environmental Considerations:
- Evaluate the impact of environmental factors such as temperature, humidity, and exposure to chemicals on fan performance and material stability.
- Select materials and design features that can withstand the intended operating conditions over the fan's lifetime.
By addressing these key elements during the design, manufacturing, and quality control processes, you can ensure the successful production of plastic injection-molded turbine fan and cooling fan parts that meet the demanding requirements of various applications, including electronics cooling, HVAC systems, automotive cooling, and industrial ventilation.
What should be cared for plastic injection molding Turbine Fan & Cooling Fan parts design?
Designing plastic injection-molded turbine fan and cooling fan parts requires careful consideration of various factors to ensure optimal performance, efficiency, and durability. Here are key aspects to focus on during the design process:
-
Airflow Efficiency:
- Optimize the fan blade design and geometry to maximize airflow and pressure generation while minimizing noise and vibration.
- Consider factors such as blade profile, angle of attack, chord length, and blade pitch to achieve the desired airflow characteristics.
- Use computational fluid dynamics (CFD) analysis to simulate airflow patterns and optimize blade design for efficiency.
-
Material Selection:
- Choose a plastic material with suitable properties for fan applications, considering factors such as heat resistance, mechanical strength, and dimensional stability.
- Select materials with good thermal conductivity or add thermally conductive fillers to enhance heat dissipation capabilities.
-
Mechanical Strength and Durability:
- Design fan parts with sufficient mechanical strength and rigidity to withstand dynamic loads, vibrations, and thermal cycling.
- Reinforce critical areas such as blade roots, hub connections, and mounting points to prevent premature failure or fatigue.
-
Heat Dissipation and Thermal Management:
- Incorporate features such as heat sinks, fins, or thermal conduction pathways to enhance heat dissipation and thermal management capabilities.
- Ensure proper airflow channels and ducting to direct airflow to areas requiring cooling.
-
Moldability and Manufacturing Considerations:
- Design parts with uniform wall thickness, smooth transitions, and minimal undercuts to facilitate mold filling and ejection.
- Consider draft angles, parting lines, and gating locations to optimize moldability and minimize molding defects.
-
Balance and Vibration Control:
- Ensure that fan blades are properly balanced to minimize vibration, noise, and wear during operation.
- Design blades with symmetrical profiles and equal weight distribution to achieve dynamic balance.
-
Assembly Compatibility:
- Design fan parts with features that facilitate assembly, mounting, and integration into cooling systems or electronic devices.
- Ensure proper alignment, fit, and compatibility with mating components and mounting hardware.
-
Surface Finish and Texture:
- Control surface finish to reduce air resistance and improve fan efficiency.
- Implement texture or surface treatments to minimize friction and turbulence on blade surfaces.
-
Environmental Considerations:
- Evaluate the impact of environmental factors such as temperature, humidity, and exposure to chemicals on fan performance and material stability.
- Select materials and design features that can withstand the intended operating conditions over the fan's lifetime.
-
Testing and Validation:
- Conduct thorough testing and validation of fan designs through prototyping and performance testing.
- Use functional testing, airflow measurements, and noise analysis to verify performance and optimize design parameters.
By addressing these key considerations during the design process, you can ensure the successful development of plastic injection-molded turbine fan and cooling fan parts that meet the demanding requirements of various applications, including electronics cooling, automotive cooling, industrial ventilation, and HVAC systems.
The plastic injection molding application for Turbine Fan & Cooling Fan
Plastic injection molding plays a crucial role in the production of turbine fans and cooling fans, providing efficient, cost-effective solutions for various applications. Here are some common applications of plastic injection-molded turbine fans and cooling fans:
-
Electronics Cooling:
- Turbine fans and cooling fans are used in electronic devices such as computers, servers, routers, and gaming consoles to dissipate heat generated by electronic components.
- These fans help maintain optimal operating temperatures, prevent overheating, and extend the lifespan of electronic devices.
-
Automotive Cooling Systems:
- Plastic injection-molded fans are used in automotive cooling systems, including radiator fans, engine cooling fans, and HVAC fans.
- These fans help regulate engine temperature, cool radiators, and provide airflow for heating, ventilation, and air conditioning systems in vehicles.
-
Industrial Ventilation:
- Turbine fans and cooling fans are employed in industrial applications for ventilation, air circulation, and cooling of machinery and equipment.
- They help remove heat, fumes, and airborne particles from industrial environments to maintain worker safety and equipment performance.
-
HVAC Systems:
- Cooling fans are integral components of heating, ventilation, and air conditioning (HVAC) systems in residential, commercial, and industrial buildings.
- These fans circulate air, regulate indoor temperatures, and improve indoor air quality for occupant comfort and health.
-
Appliance Cooling:
- Turbine fans and cooling fans are used in household appliances such as refrigerators, freezers, air conditioners, and dehumidifiers to dissipate heat generated by compressors and other components.
- They help maintain proper temperature levels, preserve food freshness, and prevent appliance malfunction due to overheating.
-
Medical Equipment Cooling:
- Plastic injection-molded fans are utilized in medical devices and equipment such as MRI machines, CT scanners, X-ray machines, and laboratory equipment for cooling critical components and systems.
- These fans ensure reliable operation, precision performance, and patient safety in medical settings.
-
Aerospace and Aviation:
- Cooling fans are used in aircraft and aerospace applications for avionics cooling, cabin ventilation, and equipment cooling.
- They help regulate temperature and airflow in aircraft cabins, cargo compartments, and electronic systems to ensure optimal performance and passenger comfort.
-
Power Generation:
- Turbine fans and cooling fans are employed in power generation facilities such as thermal power plants, nuclear power plants, and wind farms for cooling turbines, generators, and electrical equipment.
- They help dissipate heat and maintain efficient operation of power generation systems.
-
Data Centers and Server Rooms:
- Cooling fans play a critical role in data centers and server rooms to maintain optimal operating temperatures for servers, networking equipment, and storage systems.
- They help prevent equipment overheating, minimize downtime, and ensure data integrity and reliability.
-
Consumer Electronics:
- Turbine fans and cooling fans are used in various consumer electronics products such as home entertainment systems, gaming consoles, projectors, and audio amplifiers to dissipate heat generated by electronic components.
- These fans ensure reliable performance, prolong device lifespan, and enhance user experience.
Overall, plastic injection-molded turbine fans and cooling fans are essential components in a wide range of applications, providing efficient and reliable thermal management solutions for electronic devices, industrial equipment, automotive systems, and more.
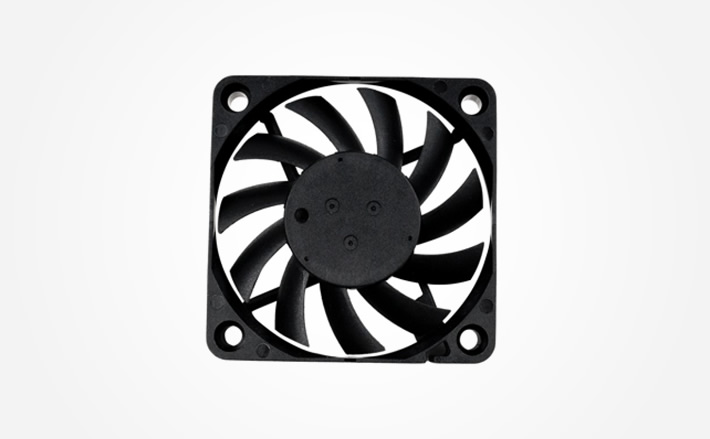
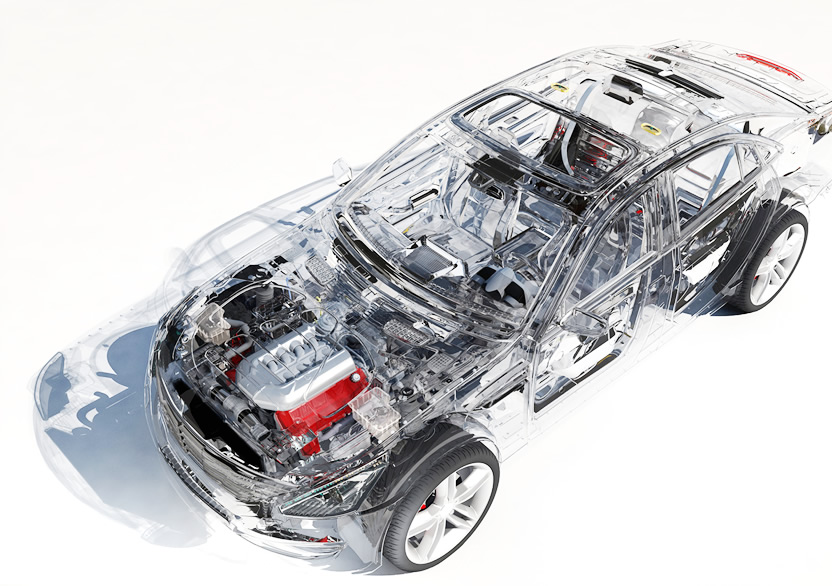
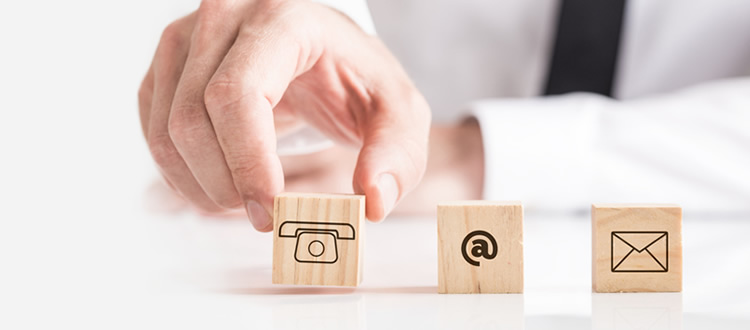