Insert Molding / Overmolding
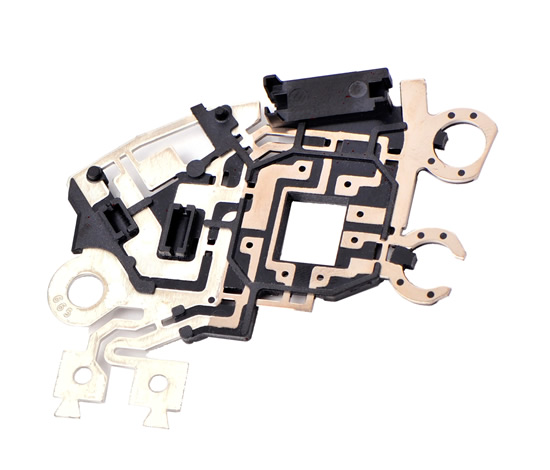
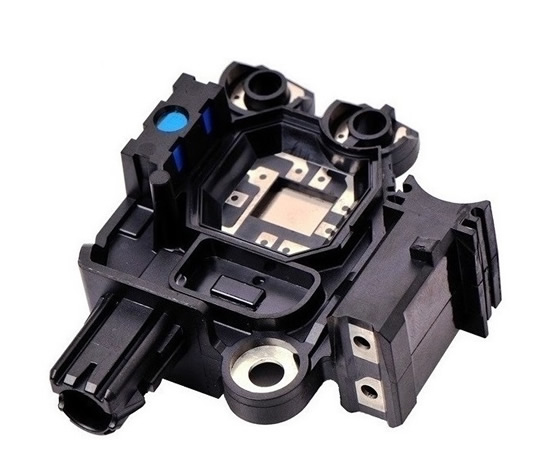
Insert Molding: Over 1000 Mold Sets and 50 Million Parts Manufactured

Material using for the insert molding / overmolding
-
• Plastic Raw Material :PPS, PPA, PBT, PET, PEI, PC, POM, Nylon PA, PA6, PA66, PA9T, LCP, Derlin, Acrylic, etc.
-
• Special Material :PEEK
For more info for Material selection, please visit "Material Selcetion for Insert Molding"
Material using for the insert
-
• Metal Meterial :Brass, Stainless steel, Aluminum, Stamping part, metal machining pins, bushing, metal coating, plating mterial, ect.
-
• Special Material :Ceramic, Glass, Chip, Wafer, Cable, PCB(printed circuit board), etc.
Jump to Section
► Insert molding and overmolding Deisgn Guidelines
► Benefits and advantage of insert molding and overmolding
► Insert molding and Overmolding considerations
► Typical insert moulded components
► Insert Molding and Overmolding Mold Design Overview
► X-ray CT 3D Scan Application on Insert Molding Parts Inspection by Ming-Li
► Insert Molding technology application for the next generation
► Overmolding offers several advantages
► For complex insert molding part, it can make pre molding first and then process overmolding
► Key elements for insert molding technology
► The new develop for insert molding technology
► Insert Molding Process Overview
► Ming-Li Capabilities of Insert Molding
► Case Study for Ming-Li Precision Insert Molding Solution
What is insert molding?
Ming-Li do have over 40 years’ experience on any kinds of insert molding molds and plastic injection parts production. Our insert molding parts are designed and manufactured for many different applications. We also have experience on IC insert molding, cable insert molding and glass insert.molding. Insert moulding is the plastic injection molding process in which a thermoplastic material is molded around an insert pieces, creating a strongly bonded, integrated assembly. We do have knowledge about metal inserts, and its coating, plating and molding expertise to reach customer request. Any problems of insert molding process, it is very welcome to contact us for more understanding.
What is overmolding?
Insert Molding vs. Overmolding
Feature | Insert Molding | Overmolding |
---|---|---|
Process Definition | Embedding a preformed insert within the plastic part. | Adding layers of plastic over an existing part. |
Insert Material | Metal, ceramic, plastic, or other materials. | Typically plastic over plastic, but can include metal. |
Application | Components requiring strong attachment to inserts. | Parts needing additional layers or multi-material use. |
Complexity | High, due to precise placement of inserts. | High, involves multiple molding steps. |
Cycle Time | Longer, requires careful handling of inserts. | Longer, due to multi-step process. |
Cost | Higher, influenced by insert material and handling. | Higher, due to additional molding steps. |
Design Flexibility | High, can incorporate various insert shapes and types. | High, allows for creative multi-material designs. |
Strength | High, strong bond between insert and molded plastic. | Variable, depends on bonding quality between layers. |
Common Uses | Electrical components, threaded parts, tools. | Grips, handles, multi-material housings. |
Tooling Requirements | Complex, needs to accommodate inserts. | Complex, needs multiple molds for different materials. |
Material Compatibility | Broad, various insert materials can be used. | Limited, typically same or compatible materials. |
- • Insert Molding: Ideal for integrating components within plastic parts, providing strength and durability.
- • Overmolding: Best for adding ergonomic features or additional layers to a base component.
Both technologies enhance the functionality and aesthetics of plastic parts, but the choice between them depends on the specific application requirements.
Overmolding and Insert Molding Design Guidelines
Our basic guidelines for overmolding and insert molding include important design considerations to help improve part manufacturability, enhance cosmetic appearance, and reduce overall production time. View our design guidelines page for more in-depth details.
Benefits and advantage of insert molding and overmolding
Metal inserts and bushings are commonly used for reinforcing the mechanical properties of the plastic parts or thermoplastic elastomer products that are created through the insert injection molding process. Insert molding provides a number of benefits that will improve your company’s processes all the way down to its bottom line. Some of the benefits of insert injection molding, include:
• Improve strength & structure
• Improve component reliability
• Reduces the part weight and size
• Reduces labor and assembly costs
• Enhance design flexibility
Insert molding and Overmolding considerations
Our experienced staffs are expert at the insert molding and overmolding process. They have the capabilities to take insert injection materials and create plastic injection inserts from those materials. However, there are certain factors that should be considered before making a final decision regarding the insert molding process. The insert molding costs must be weighed, including the insert and tooling costs. The inserts themselves also need to be able to withstand the injection molding process, as some pressures and temperatures can damage them. Other considerations that should be factored, include:
- • Means to hold the insert during the molding process
- • Bosses or undercuts that provide additional retention strength within the molded part
- • Understanding which specific components and technologies are combined into a single component within the insert injection molding process
Insert Molding Process Parameters
Parameter Name | Unit | Range or Value | Notes |
---|---|---|---|
Injection Temperature | °C | 180-343 | Depends on material |
Injection Pressure | MPa | 50-150 | Depends on mold design |
Injection Time | Seconds | 2-10 | Depends on part size |
Cooling Time | Seconds | 10-60 | Depends on material and part thickness |
Clamping Force | kN | 500-1500 | Depends on mold size |
The Insert Molding Material Properties
Material Name | Hardness | Melting Point | Shrinkage Rate | Notes |
---|---|---|---|---|
ABS | 75-85 | 105-115°C | 0.4-0.7% | General-purpose material |
PP (Polypropylene) | 85-95 | 130-170°C | 1.0-2.5% | Excellent chemical resistance |
PBT (Polybutylene Terephthalate) | 90-95 | 140-170°C | 1.5-2.5% | Toughness, solvent resistance |
PC (Polycarbonate) | 70-80 | 230-260°C | 0.5-0.7% | High impact strength |
PA Nylon | 75-90 | 190-250°C | 0.7-1.5% | High wear resistance |
PEEK | 85-90 | 343°C | 1.2-1.5% | High performance material |
PEI (Ultem) | 78-83 | 217-222°C | 0.5-0.7% | High heat resistance |
PPS (Polyphenylene Sulfide) | 80-100 | 200-240°C | 0.6~1.4% | Chemical resistance, thermal stability, mechanical strength |
The Insert Specifications for insert molding
Insert Name | Material | Dimensions | Weight | Manufacturing Method |
---|---|---|---|---|
Brass Insert | Brass | Various | Varies | Machining |
Stainless Steel Insert | Stainless Steel | Various | Varies | Machining |
Aluminum Insert | Aluminum | Various | Varies | Machining |
Ceramic Insert | Ceramic | Various | Varies | Pressing and Sintering |
Glass Insert | Glass | Various | Varies | Molding |
Metal Coating | Various Metals | Various | Varies | Plating |
Chip Insert | Silicon | Various | Varies | Fabrication |
Wafer Insert | Silicon | Various | Varies | Fabrication |
Cable Insert | Copper and Insulation | Various | Varies | Extrusion |
PCB Insert | Composite Material | Various | Varies | Lamination and Etching |
Insert Molding Production Process
Process Step | Description | Notes |
---|---|---|
Material Preparation | Prepare the required plastic granules and inserts | Ensure materials are dry |
Mold Installation | Install the mold onto the injection molding machine | Check if the mold is clean |
Insert Placement | Correctly place the inserts into the mold | Ensure the inserts are precisely positioned |
Injection Molding | The injection machine runs and fills the mold cavity with plastic | Control injection parameters |
Cooling and Ejection | After cooling, open the mold and eject the finished part | Inspect the part quality |
Quality Inspection | Check if the part meets dimensions, strength, etc. | Conduct necessary quality tests |
Our typical insert moulded components
Many industries can benefit from incorporating insert moldings into their component design. Ming-Li precision insert moulding / overmolding cover a wide industry base including military, automotive, Inverter modules, converters, power control devices, electronics, electrical, medical, life sciences, banking equipment, aerospace, marine, furniture, building components.
The types of insert moulding / overmolding manufactured include :
- • Electrical and electronic pins
- • Electrical and electronic contacts and connectors
- • Inverter modules
- • Converters
- • Power control devices
- • Auto parts
- • Switches
- • Mechanical assemblies
- • Life science sensors
- • Overmolding Motor Rotor Stator lamination stacks
- • Solenoid valve
- • Medical instruments
- • Fasteners
- • Gears
Insert Molding and Overmolding Mold Design Overview
The mold design guidelines for our basic insert moulding and overmuolding include important mold design consideration to help improve part manufacturability, increase cosmetic appearance and reduce overall production time.
Insert Molding / Overmolding is a complex endeavor, especially in light of the many variables that come into play and the possibility of reproducing mistakes in countless injection-molded copies. Ming-Li provide insert molding / overmolding services could be consulted in the early stages of part design as our expertise in the various processes can help avoid the many pitfalls that are ready and able to hamper the realization of a successful part.
In designing for insert molding / overmolding parts, a number of rules of thumb apply: overmold edges should not feather but should end abruptly and at full thickness against a stop or into an indentation. Surface texture on the overmold can significantly aid in releasing the part from the mold. It also gives the impression that the part feels softer than it actually is while disguising any flaws from the molding process. Ample draft angles help also in mold release. Mold designers need to give careful attention to gate and vent design.
There are some unique engineering challenges that designers might face when using insert molding. The advantages of added strength and versatility must be weighed against the need for a more careful design for manufacturing review. Here are some useful guidelines to consider:
- The single biggest concern is the shrinkage of the resin. This creates hoop stress around the fitting that can cause cracking over time, especially if the part is under mechanical tension. This is how you can counteract this:
- • Use resin material with a relatively low shrinkage rate.
- • Use resin material that has been strengthened with fillers.
- • Surround the insert with a larger area of plastic.
- • Support the insert with bosses and ribs.
- • Preheat the inserts before molding. This allows the resin and the insert to cool and shrink in tandem, thus relieving some of the stress between the materials.
- Use pre-manufactured inserts that have knurled surfaces to help lock them in place.
- Avoid sharp corners and use rounded profiles instead to reduce stress.
- Design the inserts so that they’re slightly recessed. This helps to avoid damaging the tool.
X-ray CT 3D Scan Application on Insert Molding Parts Inspection By Ming-Li
1. Introduction to X-ray CT 3D Scanning for Inspection
X-ray Computed Tomography (CT) 3D scanning is an advanced, non-destructive testing method used to inspect both the external and internal features of insert-molded parts. This technology creates detailed 3D images that allow for comprehensive inspection, ensuring that the parts meet strict quality standards.
2. Key Applications of X-ray CT 3D Scanning in Insert Molding Inspection
-
• Internal Structure Verification: X-ray CT scans allow manufacturers to inspect the internal placement of inserts within the molded plastic without having to cut open the part. This ensures that the inserts are correctly positioned and fully encapsulated, preventing issues like misalignment or incomplete bonding.
-
• Detection of Voids and Defects: The technology is highly effective in detecting voids, cracks, or any other internal defects that could compromise the integrity and performance of the insert-molded part. These defects are often invisible through traditional inspection methods, making X-ray CT scans particularly valuable.
-
• Dimensional Accuracy and Tolerance Checking: X-ray CT 3D scanning provides precise measurements of complex geometries within the insert-molded part, ensuring that all dimensions are within the specified tolerances. This is critical for maintaining the functionality and reliability of the part, especially in applications where precision is paramount.
-
• Material Integrity and Bonding: The technology also allows for the assessment of the bonding quality between the insert and the surrounding plastic. By analyzing the interface between different materials, X-ray CT scans can identify potential weak points or incomplete bonding that could lead to part failure.
3. Advantages of Using X-ray CT Scanning for Inspection
-
• Non-Destructive Testing: Unlike traditional methods that might require disassembly or cutting the part, X-ray CT scanning is entirely non-destructive, allowing the part to be inspected without any physical alteration.
-
• Comprehensive Analysis: The ability to generate a complete 3D image of the part provides a more thorough inspection compared to surface-level methods, ensuring that all potential issues are identified and addressed.
-
• Efficiency in Quality Control: X-ray CT scans streamline the quality control process by quickly identifying defects, reducing the need for multiple inspection steps, and minimizing the risk of undetected issues.
4. Industry Examples of X-ray CT Scanning in Insert Molding Inspection
-
• Automotive Parts: In the automotive industry, insert molding is used for components that require a combination of metal and plastic. X-ray CT scanning ensures that these components meet safety and durability standards by thoroughly inspecting internal structures and material interfaces.
-
• Medical Devices: For medical devices, where even a minor defect can have significant consequences, X-ray CT scanning provides the precision and reliability needed to ensure that all parts meet the stringent requirements of the healthcare industry.
-
• Consumer Electronics: In electronics, where the placement and integrity of conductive inserts are critical, X-ray CT scanning ensures that parts are free from defects that could affect performance, such as misalignment or incomplete encapsulation.
X-ray CT 3D scanning is a crucial technology for the inspection of insert-molded parts, offering unparalleled accuracy and reliability. By providing detailed insights into the internal structures of these parts, it helps manufacturers maintain high standards of quality, ensuring that the final products are both functional and durable.
Our Insert Molding technology application for the next generation eco-friendly automotive
The insert molding part technology is widely using on inverter, converter and power module for EV car applications recently. Ming-Li insert molding tehnology is an injection molding process in which a thermoplastic material is molded around an insert piece or pieces, creating a strongly bonded, integrated assembly. We combine knowledge about metal inserts, plating and molding expertise to create high technique parts. Selected our insert molding technique for the inverter module controling HV motor, DCDC converter and automotive secondaly battery module.
Overmolding offers several advantages that make it a desirable manufacturing process in various industries:
Enhanced Product Performance: Overmolding allows for the combination of different materials with complementary properties. For example, a rigid substrate can be encapsulated with a soft, elastomeric material to improve grip, cushioning, or impact resistance. This combination of materials can enhance the overall performance and functionality of the product.
Improved Product Durability: By providing a protective layer over a substrate, overmolding can enhance the durability and longevity of a product. The overmolded material can protect the substrate from abrasion, impact, moisture, and other environmental factors, extending the product's lifespan.
Enhanced Ergonomics and Comfort: Overmolding can add ergonomic features to products, such as soft grips and contours, which improve user comfort and reduce fatigue during prolonged use. This can be particularly beneficial for handheld tools, handles, and other products where user comfort is essential.
Customized Aesthetics: Overmolding allows for the integration of different colors, textures, and finishes, enabling designers to create visually appealing and aesthetically pleasing products. This customization can enhance brand identity and market appeal.
Reduced Assembly and Labor Costs: Overmolding combines multiple manufacturing steps into a single process, reducing the need for assembly and labor-intensive operations. This can result in cost savings and increased efficiency in production.
Design Flexibility: Overmolding offers designers greater flexibility in product design, allowing for the creation of complex shapes and geometries that would be difficult or impossible to achieve with traditional manufacturing methods. This flexibility enables the development of innovative and unique products.
Improved Sealing and Waterproofing: Overmolding can create a hermetic seal around electronic components or other sensitive parts, protecting them from moisture, dust, and other contaminants. This is particularly important in applications where waterproofing and environmental sealing are required.
Noise and Vibration Damping: Overmolding can dampen vibration and reduce noise by providing a cushioning layer between moving parts or components. This is beneficial in applications where noise reduction and vibration control are important, such as automotive components and handheld devices.
Overall, overmolding offers a versatile and effective solution for enhancing product performance, durability, aesthetics, and user experience across a wide range of industries and applications.
For complex insert molding part, it can make pre molding first and then process overmolding
In some cases, for complex insert molding parts, it might be beneficial to employ a multi-step process that involves pre-molding the insert before proceeding with the overmolding process. This approach can offer several advantages:
Optimized Insert Positioning: Pre-molding the insert can ensure precise positioning within the mold cavity before the overmolding process begins. This can be particularly important for complex parts with multiple inserts or intricate geometries where exact alignment is critical for functionality and performance.
Improved Adhesion and Bonding: Pre-molding the insert allows for better adhesion and bonding between the insert and the overmolded material. This can result in a stronger and more reliable bond, enhancing the overall durability and integrity of the part.
Reduced Insert Movement or Displacement: Pre-molding the insert can help prevent movement or displacement during the overmolding process, ensuring that the insert remains securely in place within the mold cavity. This is especially beneficial for inserts that are prone to shifting or rotating during injection molding.
Enhanced Control over Material Flow: Pre-molding the insert can help control the flow of molten plastic around the insert during the overmolding process. This can minimize the risk of air entrapment, voids, or defects in the overmolded material, resulting in a higher-quality finished part.
Streamlined Manufacturing Process: While pre-molding the insert adds an additional step to the manufacturing process, it can streamline overall production by optimizing the overmolding process and reducing the risk of rework or scrap due to insert misalignment or bonding issues.
However, it's essential to evaluate the specific requirements of the part and consider factors such as material compatibility, process complexity, production volume, and cost-effectiveness when determining whether to pre-mold inserts before overmolding. In some cases, a single-step overmolding process may be sufficient and more practical, especially for simpler parts or when time and cost constraints are significant considerations.
Key elements for insert molding technology
Mold Design: The design of the mold is crucial for insert molding. It must accommodate the insert(s) and allow for proper flow of the molten plastic around the insert(s) to achieve the desired shape and properties of the finished part. Mold design considerations include gate location, venting, cooling channels, and part ejection mechanisms.
Insert Material Selection: Selecting the appropriate insert material is essential for achieving the desired mechanical, thermal, and chemical properties of the finished part. Common insert materials include metals (e.g., brass, steel), plastics, and ceramics, chosen based on factors such as strength, conductivity, and compatibility with the overmolding material.
Overmolding Material Selection: Choosing the right overmolding material is critical for achieving the desired performance, aesthetics, and functionality of the finished part. Factors to consider include material compatibility with the insert and substrate, mechanical properties (e.g., hardness, flexibility), thermal stability, and environmental resistance.
Insert Preparation: Proper preparation of inserts is necessary to ensure good adhesion and bonding with the overmolding material. Surface treatment techniques such as cleaning, roughening, or applying adhesion-promoting agents may be required to enhance bonding between the insert and overmolded material.
Injection Molding Process Parameters: Optimizing injection molding process parameters, such as temperature, pressure, injection speed, and cooling time, is essential for achieving uniform filling of the mold cavity, minimizing defects, and ensuring dimensional accuracy and part quality.
Mold Temperature Control: Maintaining precise control over mold temperature is crucial for achieving consistent part quality and minimizing cycle times. Proper temperature control helps prevent warping, shrinkage, and other molding defects while promoting optimal material flow and part consolidation.
Quality Control and Inspection: Implementing robust quality control measures and inspection procedures is essential for ensuring the dimensional accuracy, surface finish, and mechanical properties of insert molded parts. Inspection methods may include visual inspection, dimensional measurement, and testing for material properties and adhesion strength.
Automation and Robotics: Utilizing automation and robotics in insert molding processes can enhance productivity, repeatability, and efficiency while reducing labor costs and cycle times. Automated systems can handle insert loading, part handling, and quality inspection tasks, leading to increased throughput and consistency in production.
By addressing these key elements effectively, manufacturers can optimize insert molding technology to produce high-quality parts with complex geometries, integrated features, and enhanced performance for various applications across industries.
Ming-Li ability for insert molding technology
Integration of Inserts: Insert molding involves the integration of pre-formed inserts, typically made of metal or another material, into the mold cavity before injecting molten plastic around them. This integration allows for combining the benefits of different materials into a single component.
Enhanced Strength and Functionality: By incorporating inserts into plastic parts, insert molding can enhance strength, rigidity, and functionality. Inserts can provide structural support, reinforcement, or specific features that improve the performance of the final part.
Reduced Assembly Steps: Insert molding reduces the need for assembly steps by combining multiple components into a single part. This streamlines the manufacturing process, reduces labor costs, and minimizes the risk of assembly errors.
Design Flexibility: Insert molding offers design flexibility, allowing for the creation of complex geometries, integrated features, and multi-material assemblies. Designers can achieve innovative solutions and optimize part performance to meet specific requirements.
Material Compatibility: Selecting compatible materials for both the insert and overmolded plastic is essential for achieving strong bonding and ensuring the integrity of the final part. Compatibility considerations include adhesion, thermal expansion coefficients, and chemical resistance.
Injection Molding Process Control: Precise control of injection molding process parameters, such as temperature, pressure, and injection speed, is crucial for achieving uniform filling of the mold cavity and minimizing defects. Proper process control ensures consistent part quality and dimensional accuracy.
Insert Preparation and Handling: Proper preparation and handling of inserts are necessary to ensure good adhesion and bonding with the overmolded plastic. Surface treatment techniques, such as cleaning, roughening, or applying adhesion promoters, may be required to enhance bonding.
Quality Assurance and Inspection: Implementing robust quality assurance measures and inspection procedures is essential for ensuring the dimensional accuracy, surface finish, and mechanical properties of insert molded parts. Inspection methods may include visual inspection, dimensional measurement, and testing for material properties.
Cost Considerations: While insert molding offers numerous benefits, including reduced assembly steps and enhanced part performance, manufacturers must consider the costs associated with tooling, materials, and labor. Cost-effective production strategies should be employed to optimize overall manufacturing expenses.
Application Diversity: Insert molding technology finds applications across various industries, including automotive, electronics, medical devices, consumer goods, and industrial equipment. It is suitable for producing a wide range of components, such as connectors, housings, handles, and sensors.
By understanding and effectively managing these key points, manufacturers can leverage insert molding technology to produce high-quality, cost-effective parts that meet the demanding requirements of modern applications.
Ming-Li Precision Insert Molding Automation and Robotics
The new develop for insert molding technology
Insert molding technology continues to advance, driven by the demand for more complex, integrated, and cost-effective manufacturing solutions across various industries. Here are some recent developments in insert molding technology:
-
Advanced Materials Compatibility:
- • Development of insert molding materials compatible with a wider range of substrates, including metals, ceramics, glass, and composite materials.
- • Introduction of engineered thermoplastics with enhanced adhesion properties, allowing for reliable bonding between the insert and the molded plastic material.
-
Multi-Material Insert Molding:
- • Advancements in multi-material insert molding techniques, enabling the simultaneous overmolding of multiple inserts with different materials in a single molding cycle.
- • Integration of dissimilar materials with varying properties, such as rigid and flexible plastics, to create complex components with tailored functionalities.
-
Precision Molding Processes:
- • Implementation of advanced molding processes, such as micro insert molding and nano insert molding, for producing miniature components with high precision and tight tolerances.
- • Use of high-resolution molds, micro-scale tooling, and ultra-precision machining techniques to achieve intricate features and microstructures in insert-molded parts.
-
Insert Automation and Robotics:
- • Integration of automated handling systems and robotics for precise and efficient placement of inserts into the mold cavity.
- • Use of vision systems, sensors, and feedback controls to ensure accurate positioning and alignment of inserts during the molding process, reducing cycle times and improving repeatability.
-
Embedded Electronics and Sensors:
- • Integration of electronic components, sensors, and microchips into insert-molded parts for adding intelligence, connectivity, and functionality.
- • Development of overmolding techniques for encapsulating delicate electronic components and creating hermetically sealed enclosures for harsh environments.
-
Surface Modification and Coatings:
- • Advancements in surface treatment technologies for improving adhesion between inserts and plastic materials, such as plasma treatment, corona discharge, and chemical etching.
- • Application of functional coatings and surface treatments to inserts for enhancing wear resistance, corrosion resistance, and surface finish of the molded parts.
-
In-Mold Assembly and Joining:
- • Integration of in-mold assembly and joining techniques, such as ultrasonic welding, laser welding, and heat staking, for attaching inserts to molded parts during the molding process.
- • Development of hybrid molding processes combining insert molding with in-mold assembly for producing fully assembled components in a single operation.
-
Sustainability and Recyclability:
- • Adoption of eco-friendly materials and processes for insert molding, including bio-based plastics, recycled materials, and closed-loop recycling systems.
- • Optimization of molding parameters and material formulations to minimize waste, energy consumption, and environmental impact throughout the manufacturing process.
-
Customization and Personalization:
- • Customization of insert molding solutions to meet specific customer requirements, including design flexibility, material selection, and part geometry.
- • Integration of additive manufacturing and rapid prototyping technologies for rapid iteration and customization of insert-molded parts in product development cycles.
These developments in insert molding technology are driving innovation in industries such as automotive, electronics, medical devices, consumer goods, and aerospace, enabling the production of more complex, functional, and integrated components with improved performance and cost-efficiency. Continued research and development efforts are expected to further enhance the capabilities and applications of insert molding technology in the future.
Insert Molding Process Overview
1. Design and Material Selection:
- • The process begins with precise design planning where the compatibility of materials between the insert and the plastic is crucial. Engineers select materials that complement each other to ensure that the thermal and chemical bonding between them is optimal. Common materials for inserts include metals, ceramics, and high-performance plastics.
2. Insert Preparation:
- • Preformed inserts are prepared by cleaning and sometimes pre-treating them to improve adhesion with the molten plastic. This step is vital to prevent any contaminants from affecting the molding process. Depending on the application, inserts can also be coated or primed.
3. Mold Setup:
- • Specialized molds are designed and constructed to accommodate the inserts. These molds must not only fit the insert precisely but also allow for easy placement and proper alignment during the molding process.
4. Injection Molding:
- • The plastic material is heated to its molten state and injected into the mold, where it encapsulates the insert. This stage requires precise control of injection parameters like pressure, temperature, and injection speed to ensure quality and consistency.
5. Cooling and Solidification:
- • After the plastic is injected, it needs to cool and solidify around the insert. Cooling systems within the mold draw heat out of the plastic, ensuring it solidifies correctly and the dimensions of the finished part are maintained.
6. Ejection and Finishing:
- • Once the plastic has solidified, the finished part is ejected from the mold. Post-processing steps may include trimming excess material, polishing, or painting the part to enhance its appearance or performance.
This enhanced process flow provides a comprehensive understanding of each phase in insert molding, highlighting the technical nuances that ensure the success of the manufacturing process.
Ming-Li Capabilities of Insert Molding
Ming-Li Precision demonstrates exceptional capabilities in insert molding, integrating advanced plastic injection molding techniques, precision mold design and manufacturing, and a comprehensive Total Quality Management (TQM) system. With over 1,000 sets of insert molding molds produced and more than 50 million insert-molded parts manufactured, Ming-Li is a trusted partner for global leaders seeking high-quality insert-molded products.
-
• In-house CPK Rate :≧ 1.33
-
• Tolerance Range :Up to +/-0.01mm
-
• Mold Size :600L*600W*600H ; up to 2,000kgs
-
• Monthly Capacity :20 sets Molds / Toolings / Dies ; 8 million pcs / Overmolding & insert molding Injection parts
Ming-Li Capabilities in Insert Molding
Item | Description |
---|---|
Insert Molding Mold Experience | Over 1,000 sets of insert molding molds produced |
Insert Molding Manufacturing Experience | Over 50 million insert-molded parts manufactured |
Vertical Injection Machines | Tonnage Range: 35T to 250T Maximum Product Size: 8.5 x 11 x 6 inches (216 x 279 x 150 mm) |
Horizontal Injection Machines | Tonnage Range: 60T to 200T Maximum Product Weight: 0.1g to 500g |
Mold Precision | Mold Precision: ± 0.0015mm Product Precision: ± 0.01~0.05mm |
Design and Manufacturing Support | Comprehensive support from concept design to final product delivery Uses Autodesk Moldflow for mold flow analysis |
Mold Maintenance and Management | Regular inspections, precise adjustments, and necessary repairs Ensures molds remain in optimal condition throughout their lifecycle |
Quality and Environmental Management Certifications | ISO / IATF 16949 certification |
Injection Machines and Equipment
Ming-Li’s insert molding capabilities are supported by a wide range of state-of-the-art vertical and horizontal injection machines, enabling the production of diverse product sizes and weights:
-
- • Tonnage Range: 35T to 250T
- • Maximum Product Size:
- Inches: 8.5 x 11 x 6
- Millimeters: 216 x 279 x 150
- • Precision:
- Mold: ± 0.0015mm
- Product: ± 0.02~0.05mm
-
- • Tonnage Range: 15T to 320T
- • Maximum Product Weight: 0.1g~500g
Comprehensive Services and Expertise
-
Precision Injection Mold Design and Manufacturing:
- Ming-Li designs and manufactures high-precision injection molds that ensure accurate positioning and embedding of inserts within plastic parts. With experience in producing over 1,000 sets of insert molding molds, these molds are tailored to the specific needs of each application, ensuring optimal performance and long-term reliability. Ming-Li’s engineering team collaborates closely with clients to identify potential design or manufacturability issues early in the process, optimizing production and reducing costs.
-
Advanced Injection Molding Technology:
- Utilizing cutting-edge injection molding technologies, Ming-Li has manufactured over 50 million high-quality insert-molded parts. These technologies are overseen by a team of experienced injection molding engineers, ensuring that each production step adheres to strict quality control standards. Ming-Li’s capabilities allow for the production of parts with complex geometries, ensuring precision and durability.
-
Mold Maintenance and Management:
- Ming-Li provides comprehensive mold maintenance services to ensure that molds remain in optimal condition throughout their lifecycle. This includes regular inspections, precise adjustments, and necessary repairs, ensuring consistent quality and long-term stability in production.
-
Custom Solutions and Design Support:
- Ming-Li offers full design support and custom solutions, from concept design to final product delivery. The company utilizes tools such as Autodesk Moldflow for mold flow analysis to help clients optimize designs, improve manufacturability, and enhance product performance. This ensures that each product meets the specific requirements of its application.
-
Quality and Environmental Management Certifications:
- Ming-Li’s commitment to quality is reflected in its multiple international certifications, including ISO / IATF 16949.
Ming-Li Precision’s insert molding capabilities are comprehensive, covering everything from precision mold design to advanced injection molding technology. With over 1,000 sets of insert molding molds produced and more than 50 million insert-molded parts manufactured, Ming-Li has established itself as a leader in the field. The company’s strong commitment to quality and technical expertise makes it the ideal partner for manufacturers looking to produce high-precision, durable, and environmentally compliant insert-molded products. Beyond efficient manufacturing services, Ming-Li offers extensive support in design, optimization, and environmental responsibility, ensuring that all client needs are fully met.
Case Study for Ming-Li Precision Insert Molding Solution
Case Study 1: Automotive Connector Overmolding
Challenge:
An automotive manufacturer needed durable connectors capable of withstanding high temperatures, vibrations, and chemical exposure.
Solution:
Ming-Li Precision utilized their advanced insert molding capabilities to overmold metal inserts with high-performance plastic, ensuring a strong bond and excellent protection for the connectors.
Outcome:
The overmolded connectors met all durability and performance requirements, resulting in improved reliability and extended product life in automotive applications.
Case Study 2: Medical Device Housing
Challenge:
A medical device company required precise and durable housings for their diagnostic equipment to ensure proper fit for electronic components and withstand frequent use.
Solution:
Ming-Li Precision used insert molding to integrate metal inserts into plastic housings, providing precise alignment and enhanced structural integrity.
Outcome:
The housings offered reliable performance, precise fit, and durability, enhancing the overall quality and longevity of the diagnostic equipment.
Case Study 3: Consumer Electronics Enclosures
Challenge:
A consumer electronics firm sought robust and aesthetically pleasing enclosures for a new line of handheld devices, incorporating metal inserts for added strength and functionality.
Solution:
Ming-Li Precision's insert molding process allowed for seamless integration of metal inserts within plastic enclosures, achieving the desired strength and aesthetic appeal.
Outcome:
The resulting enclosures were strong, durable, and visually appealing, leading to high customer satisfaction and a successful product launch.
These case studies showcase Ming-Li Precision's expertise in delivering high-quality, reliable, and customized insert molding solutions across various industries.
Ming-Li Insert Molding Project Example
Further Reading
For those interested in diving deeper into the latest technologies and trends in insert molding, the following resources offer comprehensive insights:
► Insert Molding Tech in Ming-Li company
► The Overmolding Tech in Ming-Li company
► The common Inserts Materials for Insert Molding
► The Latest Technologies and Trends for Insert Molding
► The Insert Molding Common Materials and Their Properties
► Insert Molding / Overmolding application in Ming-Li Precision
► LSR Insert Molding / Overmolding (P+R) Technology
► Advanced Induction Coil Insert Molding Technology
► Press-Fit(Fish-Eye) Terminal Insert Molding Technology
► Silicon Steel Sheet Insert Molding Technology
► Capacitor and Resistor Insert Molding Technology
► Magnet Insert Molding Technology
Further understanding for Insert Molding / Overmolding
This is just a partial overview of insert molding and overmolding. Are they the right solutions for you? Not sure how to apply them to your next project? Just contact our technical experts and we can offer helpful advice about how to get the best results from both processes.
Leading of insert molding/ overmolding ... in the field of insert molding Ming-Li precision
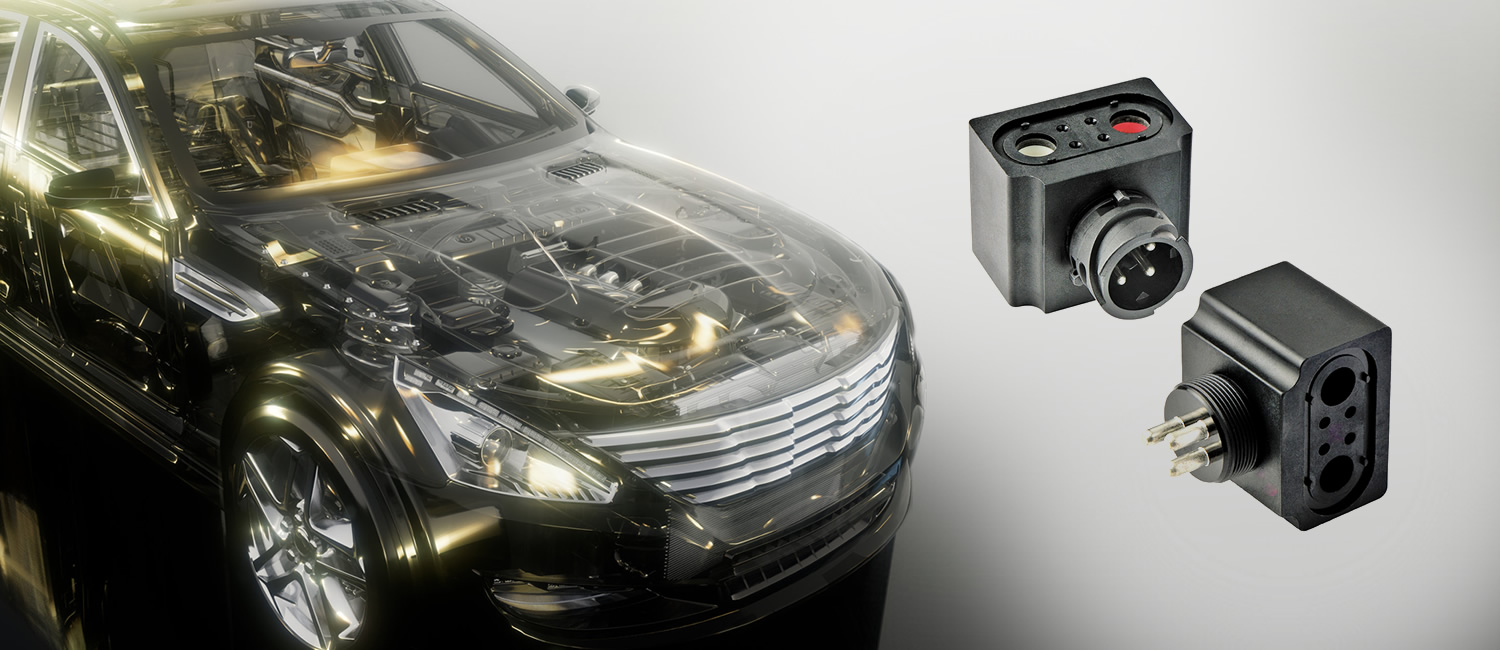