Automotive

Ming-Li Automotive Proudcts
Application Areas
Plastic injection molding is a highly versatile manufacturing process widely used in the automotive industry to produce a variety of components. This method involves injecting molten plastic into a mold cavity where it cools and solidifies into the desired shape. Here are some key automotive components made using plastic injection molding:
Plastic Injection Molding Applications in Automotive Components
-
Interior Components:
- Dashboard Panels: Injection molding is used to create the complex shapes of dashboard panels, including integrated air vents and glove compartments. These components often use durable plastics like ABS (Acrylonitrile Butadiene Styrene) and polycarbonate.
- Door Panels and Trims: Door panels and various interior trims, including those with integrated features such as armrests and storage pockets, are commonly produced using injection molding.
- Center Consoles: The center console, which may house cup holders, gear shift surrounds, and storage compartments, is typically made through injection molding for precision and durability.
-
Exterior Components:
- Bumpers: Modern car bumpers are often made from thermoplastic materials using injection molding. This allows for the integration of complex shapes, reinforcement structures, and attachment points.
- Grilles: The front grille of a vehicle, which may feature intricate designs and need to be durable, lightweight, and impact-resistant, is often produced using injection molding.
- Mirror Housings: Side mirror housings made from molded plastic offer lightweight and durable protection for the mirrors and integrated electronics.
-
Under-the-Hood Components:
- Engine Covers: Engine covers made from molded plastic help reduce weight and can be designed to dampen noise and vibration.
- Battery Housings: Plastic injection molding is used to create durable and heat-resistant housings for car batteries, ensuring safety and longevity.
- Air Intake Manifolds: These components direct air into the engine's cylinders and are often made from plastic to reduce weight and resist corrosion.
-
Functional and Structural Parts:
- Brackets and Mounts: Various brackets and mounts throughout the vehicle, including those for securing electronics, sensors, and other components, are commonly made from injection-molded plastic.
- Fasteners and Clips: Small but essential components like clips, fasteners, and retainers used throughout the vehicle are produced using injection molding for high precision and repeatability.
Advantages of Plastic Injection Molding for Automotive Components
- Cost Efficiency: Injection molding allows for high-volume production at a lower cost per part, making it ideal for the automotive industry.
- Weight Reduction: Plastic components are lighter than their metal counterparts, contributing to overall vehicle weight reduction and improved fuel efficiency.
- Design Flexibility: The process allows for the creation of complex shapes and integrated features that would be difficult or impossible to achieve with other manufacturing methods.
- Durability: Modern engineering plastics are highly durable, offering excellent resistance to impact, heat, and chemicals.
- Consistency and Precision: Injection molding produces parts with very tight tolerances, ensuring consistency and high quality across large production runs.
Starting from hybrid PCB production for automotive sensors in fuel tank in late 1970s, Ming-Li has been manufacturing automotive products for more than 30 years. Since then, we have continuously built up our design capabilities in voltage regulators, rectifiers, motor controllers, exterior LED lightings, IEPB (Integrated Electric Parking Brake) control unit etc.
Based on these experiences, our customers recognize our expertise in automotive requirements from development to manufacturing phases. Under EMS service, Ming-Li offers reliable products with robust manufacturing process, test plan and quality gating with optimized process flow for cost saving.
Plastic injection molding plays a critical role in the automotive industry, providing manufacturers with a versatile and cost-effective method for producing a wide range of components and parts. Here are some common automotive applications of plastic injection molding:
-
Interior Components: Plastic injection molding is used extensively to produce various interior components, including:
- Dashboard panels, instrument clusters, and center consoles.
- Door panels, armrests, and trim pieces.
- Seat components such as headrests, seat backs, and seat frames.
- HVAC (heating, ventilation, and air conditioning) vents, ducts, and controls.
- Storage compartments, cup holders, and console organizers.
-
Exterior Components: Plastic injection molding is utilized for manufacturing numerous exterior components, such as:
- Bumpers, bumper fascias, and bumper reinforcements.
- Grilles, grille inserts, and front-end modules.
- Body panels, fenders, and wheel arch liners.
- Side mirrors, mirror housings, and mirror mounts.
- Spoilers, aerodynamic components, and body trim.
-
Lighting Systems: Plastic injection molding is essential for producing various lighting components and systems, including:
- Headlamp lenses, housings, and reflectors.
- Taillight lenses, housings, and assemblies.
- Turn signal lenses, side marker lenses, and fog lamp housings.
- LED light guides, diffusers, and light pipes.
- Interior lighting components such as dome lights and map lights.
-
Under-the-Hood Components: Plastic injection molding is used for manufacturing several under-the-hood components, including:
- Engine covers, air intake manifolds, and engine mounts.
- Radiator grilles, cooling fans, and shrouds.
- Fluid reservoirs, caps, and tanks for coolant, windshield washer fluid, and brake fluid.
- Engine and transmission mounts, brackets, and supports.
-
Functional Components: Plastic injection molding is employed for producing various functional components and systems, including:
- Fuel system components such as fuel filler caps, fuel tanks, and fuel pump housings.
- HVAC system components such as air vents, blower motor housings, and air ducts.
- Suspension system components such as bushings, mounts, and isolators.
- Electrical connectors, sensor housings, and wiring harness components.
-
Safety and Interior Features: Plastic injection molding is used for producing safety-related components and interior features, such as:
- Airbag housings, covers, and brackets.
- Seatbelt components such as buckles, retractors, and adjusters.
- Child safety seat components such as anchors, latches, and restraints.
- Trim components such as pillar covers, headliner panels, and door seals.
Overall, plastic injection molding is integral to the automotive industry, enabling manufacturers to produce lightweight, durable, and cost-effective components with intricate designs, tight tolerances, and consistent quality.
Airconditioning
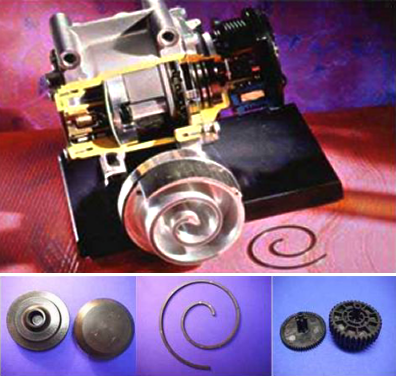
- Toughness
- No influence of moisture
- Creep resistance
- Wear resistance
- No outgassing
- Scroll seals
- Swash plates
- Gear mode door control
- Piston shoes
Electronics
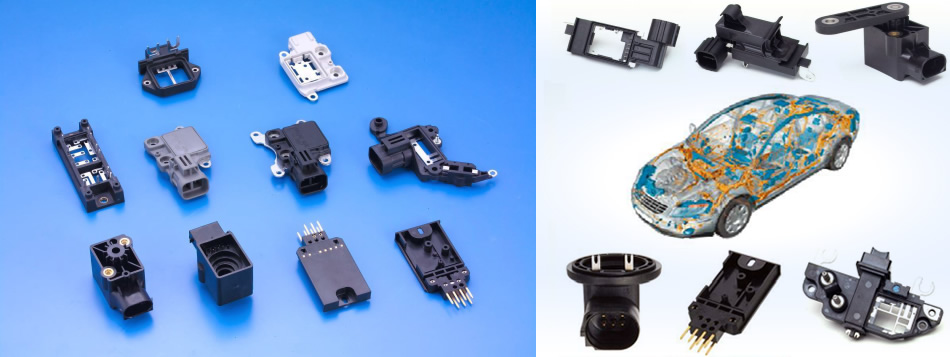
- V-O rating
- Halogen free
- Stable electrical properties
- Glow wire test confirmation
- High heat resistance
- Connectors
- Wire & Cable insulation
- Cable protection
- Printed circuit boards
- Sensor housings
Bearing Cages

- Wear resistance
- Dynamic loads applicable
- Good weld line strength
- High ductility
- Grease resistance
- No water uptake
- Competitive pricing
- Deep grooved ball bearings
- Needle bearings
- Cylindrical roller bearings
Brake
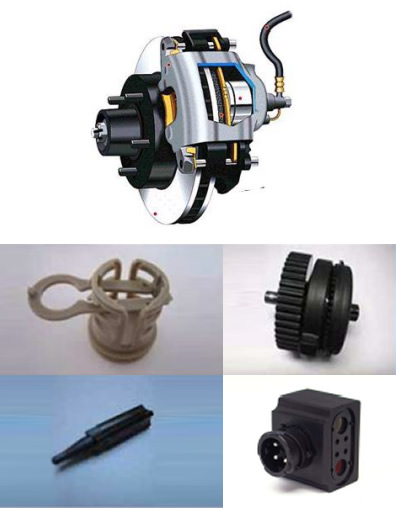
- High compressive strength
- High temperature resistance
- Good dynamic fatigue
- Cheep mass production
- Tight tolerances
- No moisture uptake
- No failure (0ppm)
- Tappets, Popppet’s & Plungers
- EPB actuation gears
- Brake wear indicators
- Supporting rings
- Brake booster sleeve + clip
Commercialized Automotive parts


Damper / Clutch
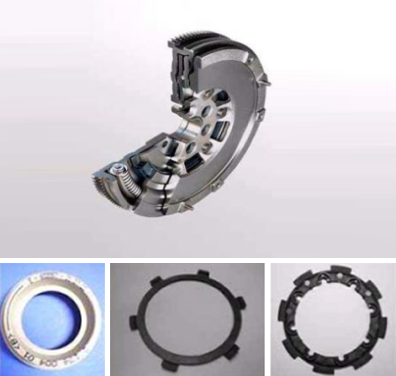
- Wear resistance
- Dynameic loads applicable
- Stable coefficient of friction
- No squeaking
- Tight tolerances
- Competitive pricing
- Dust caps
- Seal rings
- Friction washer
- Clutch rings
Door Modules
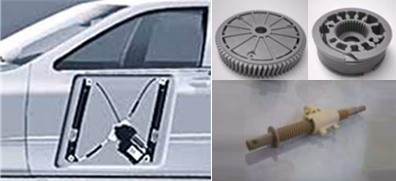
- Toughness
- No influence of moisture
- Creep resistance
- Wear resistance
- Low coefficient of friction
- Worm gear window lift
- Thrust pin electric motor
- Cable roller window lift
- Spoiler adjustment
Drivetrain
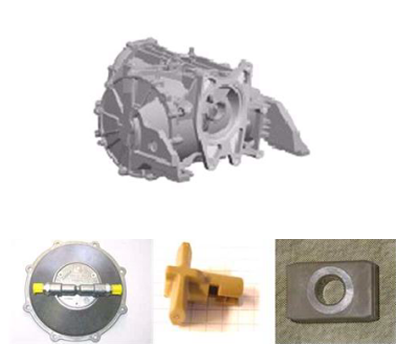
- Wear resistance
- Dynamic loads applicable
- High efficiency
- Oil resistance
- Low coefficient of friction
- Tight tolerances
- Competitive pricing
- Oil pump
- Sliding elements
Engine
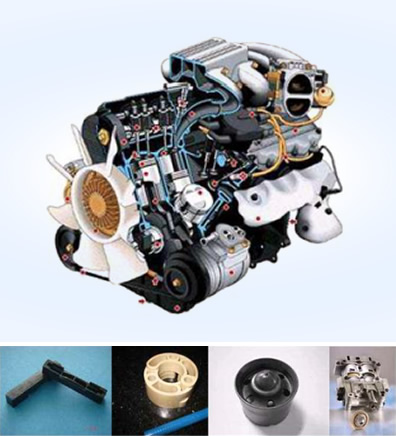
- Wear resistance
- Dynamic loads applicable
- No squeaking
- High efficiency
- Engine oil resistance
- Low weight
- Tight tolerances
- Competitive pricing
- Gears
- Thrust washer
- Gaskets
- Bearings
- Bushings
- Cam phaser
- Pumps
Exhaust Treatment

- Heat resistance
- AdBule resistance
- Wear resistance
- Exhaust condensate resistance
- Maintennance free
- Competitive pricing
- EGR actuator gears
- EGR bushings
- AdBlue diffuser
- Solenoid valves
- Bearing retainers
Fuel Management
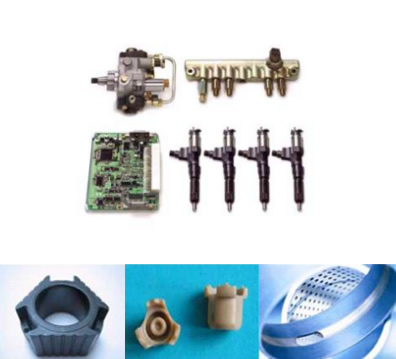
- Fuel resistance
- High pressure resistance
- Good dynamic fatigue
- Cheap mass production
- Tightest tolerances
- Wear resistance
- No failure (0pmm)
- Injector valve seats
- Pump bushing
- Seals
Ming-Li Automotive product Application Areas
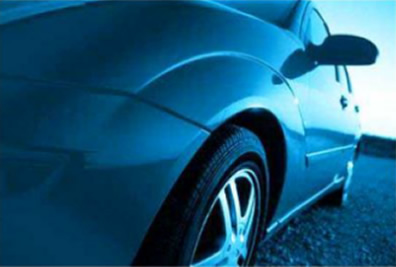
- Fuel management
- Exhaust
- Drivetrain
- Damper / Clutch
- Lighting
- Small motors
- Steering / Suspension
- Brakes
- Pumps
- Electronic / Sensors
- Seat adjustment
- Transmission
- Engine
- Door modules
Lighting
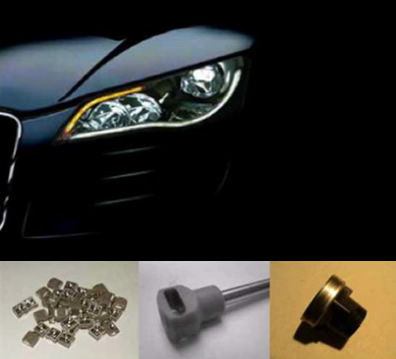
- High temperature resistance
- No influence of moisture
- Creep resistance
- Wear resistance (AFL)
- No out gassing
- Reflector housings
- Lamp socket
- Xenon light adjustor
- HB LED’s
Seat adjustment (electrical)
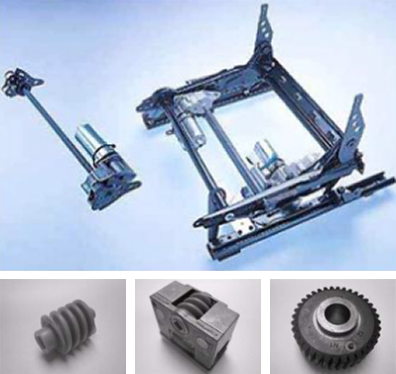
- No squeaking
- Ductile crash behavior
- Highly loadable
- Cheap mass production
- Tight tolerances
- No moisture uptake
- No issues with stress cracking
- Worm gears
- Gears
- Bushings
Steering / Suspension

- Wear resistance
- Compressive loads applicable
- No squeaking
- Tight tolerances
- No moisture uptake
- Heat resistance up to 250°C
- Seals
- Bearings shells
- Yoke bearings
- Adjustment nuts
Engine
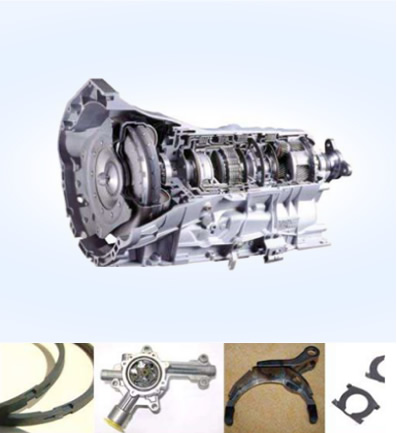
- Wear resistance
- Dynamic loads applicable
- No squeaking
- High efficiency
- Transmission oil resistance
- Low coefficient of friction
- Tight tolerances
- Competitive pricing
- Seal rings
- Thrust washer & plates
- Pad follower
- Bearing retainer, cages
- Bearings, bushings
- Shift fork pads
- oil pumps
Vacuum Pump

- Wear resistance
- Dynamic loads applicable
- Low wear over lifetime
- High efficiency
- Engine oil resistance
- Low moment of inertia
- Tight tolerances
- Thermal expansion in-line with housing
- Vane tips
- Full plastic vanes
- 2K vane tips